Applications
- The Mixproof valve is a completely hygienic double sealing valve.
- This system allows for the simultaneous processes in the two bodies of the valve by providing interface between the two fluids, preventing the possibility of product contamination.
- The leakage chamber and the leakage detector can be cleaned by "cavity spray".
- Manifolding is one of the applications of these valves in the food-processing industries, especially in the beverage and dairy industries.
Operating Principles
- When the valve is open the fluid can pass from one body to the other.
- Once the valve is closed, the double seat creates an annular chamber that isolates the bodies sealing them with double seals. It allows a CIP operation providing an interface between the two fluids, preventing the possibility of product contamination.
- Due to the leakage detector any leak of a seat seal is detected by the appearance of liquid at the bottom of the valve.
- The leakage chamber and the leakage detection system are usually cleaned by CIP without interruption of the main process.
- The area between the seats is cleaned by the introduction of the CIP fluid from an external source. Nozzles situated near the base of the lower poppet direct j ets of CIP fluid onto the leakage chamber wall. The fluid is released down the drain tube.
- The valve is designed with over-pressure protection and prevent the fluctuation of water pressure to 30bar.
|
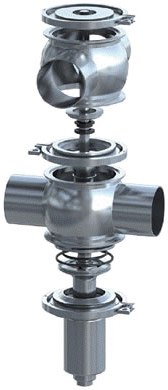 |
Design and features
- Available from DN40 - 1 1/2" to DN100 - 4".
- Valves with normally closed pneumatic actuator.
- Forged spherical bodies.
- Compact design.
- Angular orientation 360°.
- Judge whether the gasket is broken by observing whether the liquid flows out on the bottom of the valve.
- Easy disassembly by releasing the clamp. Weld connections (mm or inches).
- Balanced protection design
Options
- Gaskets: NBR and FPM (Viton(R)).
- Connections: DIN, SMS, Clamp, RJT…
- Control box C-TOP: electric connection, AS-I bus connection
- Surface finish: Ra 0.4 μm.
- Mixed body sizes: combinations of bodies with different diameters.
Materials
- Parts in contact with the media: AISI 316L
- Other stainless steel parts: AISI 304
- Internal surface finish: Ra ≤0,8 μm
- Gasket (standard): EPDM in compliance with FDA 177.2600
Technical specifications
- Max. operating pressure: 10bar (for DN4"-DN100 valves - max5bar)
- Min. operating pressure: Absolute vacuum
- Working temperature: -10℃ to 120℃ (140℃ for short periods or sterilisation)
- Compressed air pressure: 5,5bar - 7bar
- Air supply connections: R1/8" (BSP)
|
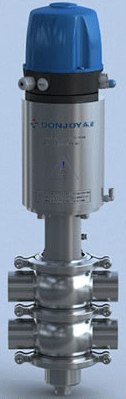 |
Cavity Spray Schematic diagram
- CIP connection for cleaning of the chamber.
- Leakage detection. Any leak of a seat seal is detected by the appearance of liquid.During the CIP process of the cavity area, the product drains down the leakage detector.